FREIGHT SHUTTLE SIGNS AGREEMENT WITH PORT HOUSTON FOR GREEN INFRASTRUCTURE PROJECT
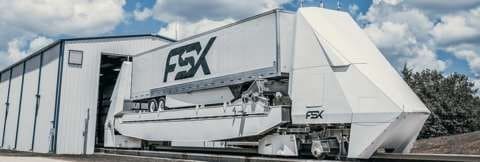
-FSX, LLC, the developer of the Freight Shuttle System and Port Houston, have entered into an agreement to explore the steps required for deployment of Freight Shuttle’s Seaport System at the Port’s growing container facilities. The Freight Shuttle is an elevated, zero emission system for moving shipping containers to and from the Port’s busy terminals, making best use of available space and addressing the need to improve air quality in the region.
The Freight Shuttle (FSX) has been developed to provide a low-emission alternative to moving freight in heavy freight corridors or ports of entry. Freight Shuttle moves truck trailers, domestic intermodal containers (up to 53 ft.), and all sizes of ocean shipping containers via emissions-free, electric-powered transporters on elevated guideways in highway or other rights-of-way over distances of up to 500 miles.
PORTS AND CRUISE LINES EXPLORE PACIFIC NORTHWEST-ALASKA GREEN CORRIDOR
Ports ranging from Seattle and Vancouver to Juneau, Alaska which make up one of the most densely operated cruise routes announced plans to work with the cruise industry to explore one of the first green corridors for shipping. Calling their effort The First Mover Commitment, the three ports, three major cruise corporations, and the cruise industry trade association supported by three maritime forums announced their effort to explore the feasibly of the world’s first cruise-led green shipping corridor.
The collaborative effort is aimed at exploring the feasibility of a green corridor that could accelerate the deployment of zero greenhouse gas emission ships and operations between Alaska, British Columbia, and Washington. The organizers highlighted that Alaska hosts more than 600 cruise sailings per year, with nearly 300 ships departing Seattle for Alaska in a six-month cruise season. While the effort is being led in collaboration with the cruise industry, this initiative said it would welcome participation from all sectors of the maritime industry and other regional ports. Domestic cargo lines, ferries, commercial fishing, tug, and barges, and other ports have a strong interest and shared goals around climate action and they would welcome an expanded agreement to reflect new participants or corridors in the region.
First Mover partners include the Port of Seattle, City and Borough of Juneau, Vancouver Fraser Port Authority, along with Carnival Corporation, Norwegian Cruise Line Holdings, Royal Caribbean Group, and Cruise Lines International Association, with the support of the Global Maritime Forum, Blue Sky Maritime Coalition, and Washington Maritime Blue. They will seek to leverage and support each other’s decarbonization work already underway and bring those resources and technological advancements to this effort.
They agreed to work together to explore the feasibility of a green corridor in the Pacific Northwest while enhancing and supporting the emission-reduction efforts already underway. The group will work collaboratively to define the governance structures, terms, and frameworks needed to guide this regional effort and look to use the green corridor as a testbed for low and zero greenhouse gas technologies and ships.
This new initiative in the Pacific Northwest joins other previously announced efforts. Shanghai and Los Angeles announced plans for the world’s first corridor and since then other initiatives have been launched around Singapore as well as by the ports of the Baltic and Northern Europe. The cruise liens follow another industry group, the Australian miners and bulk shipping companies which committed to exploring an Australia to Asia corridor.
The signatories to the declaration at COP26 pledged to support the creation of at least half a dozen green corridors by the middle of the decade. Their ambition is to scale up and expand the scope of the initiative by 2030.
TECHNOLOGY HELPING SHIPPERS TRACK, TRIM DETENTION TIME
US shippers and their logistics partners are increasingly turning to technology to reduce truck driver detention, one of the leading landside causes of supply chain disruption. Detention times that can stretch into hours and even days was the leading concern among truck drivers surveyed last year by the American Transportation
Detention has been a problem, and a potential target of US regulators, for years, but truck driver delays have become much more disruptive, and costly, during the COVID-19 pandemic. Their impact cascades across supply chains, throwing off delivery schedules that likely already were disrupted because of supply shortages, lack of capacity at critical points, and a scarcity of labor.
Even before the pandemic, the US Federal Motor Carrier Safety Administration (FMCSA) estimated that driver detention — not to be confused with detention and demurrage fees for ocean container storage and usage — cost truck drivers more than $1 billion in lost revenue a year. The FMCSA launched a new investigation of driver detention and its impact on safety, using electronic logging device (ELD) data, in January, as required by the $1.2 trillion infrastructure spending act last year.
One difficulty in fighting detention is it has multiple potential causes. “We pay out more in detention [time to drivers and carriers] than we used to,” Charles Miller, executive vice president of Evans Transportation Services, told JOC.com. “Labor shortages are a huge piece of that. But there’s also inventory congestion; there’s no warehouse space. All these things combine to cause more delays.”
US motor carrier regulations require interstate truck drivers to speak enough English to “sufficiently converse with the general public,” complete reports and recordkeeping, and answer questions from police and other officials. But compliance with that rule — and the amount of English considered “sufficient” — may be stretched in major ports and hubs from California to New Jersey.
NO ONE IS CLOSER TO THE ILWU NEGOTIATIONS
On top of two years of near perpetual port disruption due to COVID-19 and its impact on the supply chain, now, unfortunately for shippers, comes the possibility for even more. US West Coast longshore labor negotiations began on May 10; going back to the 1990s there has not been a single contract negotiation between the dockworkers and employers that hasn’t resulted in some disruption at West Coast ports. Shippers can only hope that the labor-management camaraderie seen on the docks during the worst of the pandemic and intense interest by the Biden Administration in avoiding further disruption translates into constructive talks. Yet, fears are already running high and importers are already shifting thousands of containers to the East and Gulf coasts–seen clearly in the data. No journalists are closer to the situation or more deeply connected to key players during this pivotal time than the team at The Journal of Commerce, part of S&P Global Market Intelligence.